Exploring the exciting world of manufacturing, automation plays a key role in boosting efficiency, accuracy, and safety. Our newest innovation shines a spotlight on a state-of-the-art automation solution featuring the Fanuc M-710iC/50 robot paired with the advanced IR 2D Vision package. This blog takes a deep dive into the details of our setup, highlighting the technology used and the process our team used to create this solution!
System Overview: Central to our solution is the Fanuc M-710iC/50 robot, integrated with IR Vision for precise part identification and manipulation. We've engineered a tailor-made gripper solution shown below.
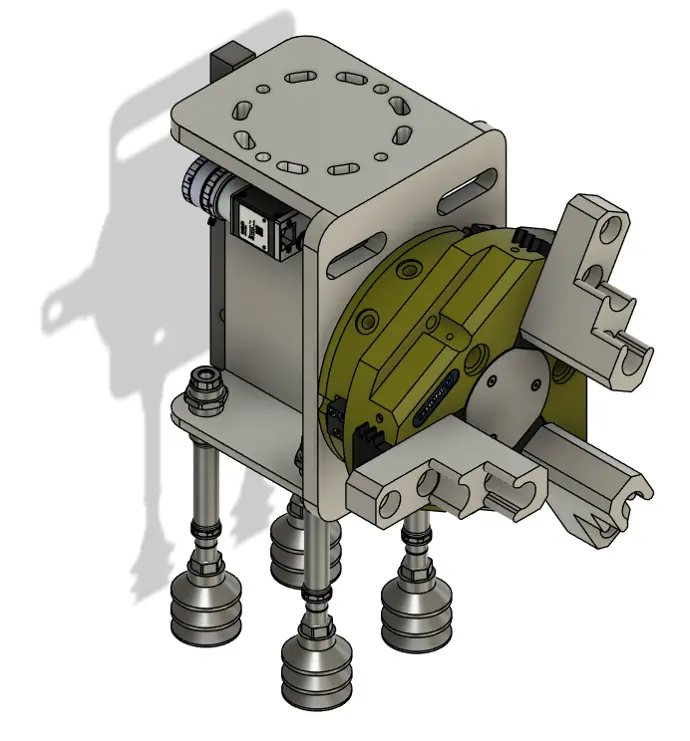
- Concentric Pneumatic Gripper: Designed for precise part handling from the inside diameter (ID).
- Suction Cup Gripper: Facilitates the placement of cardboard sheets between layers on the outfeed pallet.
- Custom Pneumatic Push Plate: Ensures accurate part seating in the CNC lathe.
The gripper system integrates seamlessly with Fanuc's IR 2D Vision software, optimizing part handling precision.
Hardware Utilized: Our automation solution leverages these essential hardware components:
- Fanuc M-710iC/50 Robot
- IR 2D Vision Package w/ Camera Lense
- Custom Gripper Solution (Concentric pneumatic gripper, Suction cup gripper, Custom pneumatic push plate)
- WAGO HMI & PLC: Enables dynamic part dimension setup and operational parameter adjustments.
- Safety Perimeter Gate and Light Curtain: Ensures operational safety by halting robot movement upon breach.
Integration: The Karel programming language is a high-level language used for programming and controlling robotic systems, emphasizing simplicity and ease of use for automation tasks.
Our automation solution integrates the Fanuc M-710iC/50 robot with the Haas CNC lathe using a custom Karel program. This software enables direct communication between the robot and CNC, allowing real-time access to control functions and status updates.
This integration ensures precise coordination during operations, enhancing efficiency and accuracy in part handling and machining processes. It represents our commitment to delivering advanced manufacturing automation solutions.
Automation Process: Our automation process is carefully designed to unfold in precise steps:
- Loading the Cell: Operators load a full pallet of parts (up to 3 layers high) at the infeed and an empty pallet at the outfeed.
- HMI Setup: Operators use the WAGO HMI to configure part quantities, select IDs, and confirm safety protocols before initiating operations.
- Robot Operation: Upon activation, the robot utilizes vision guidance to locate parts on the infeed, adjusting for offsets from the HMI.
- Part Handling:
- The robot picks and transfers each part to the CNC lathe for machining.
- A push plate mechanism ensures proper part seating before commencing CNC operations.
- The custom Karel program facilitates communication between the robot and CNC for operational tasks.
- Post-Machining:
- After machining, the robot retrieves and positions completed parts on the outfeed pallet.
- For completed layers, the robot uses the suction gripper to place cardboard sheets atop the pallet.
- Cycle Completion: This sequence repeats until all infeed parts are processed and placed on the outfeed pallet.
Conclusion: Our automation solution exemplifies how advanced robotics and customized engineering can elevate manufacturing processes. By integrating the Fanuc M-710iC/50 with IR Vision and a tailored gripper system, we achieved precision and efficiency in CNC Machine Tending. The inclusion of a WAGO HMI & PLC for dynamic setup and the custom Karel program for CNC integration further improves the system's capabilities, providing a reliable solution for the challenges faced in modern manufacturing.
Interested in a similar automation solution?
Connect with us to explore how we can propel your next manufacturing project forward!